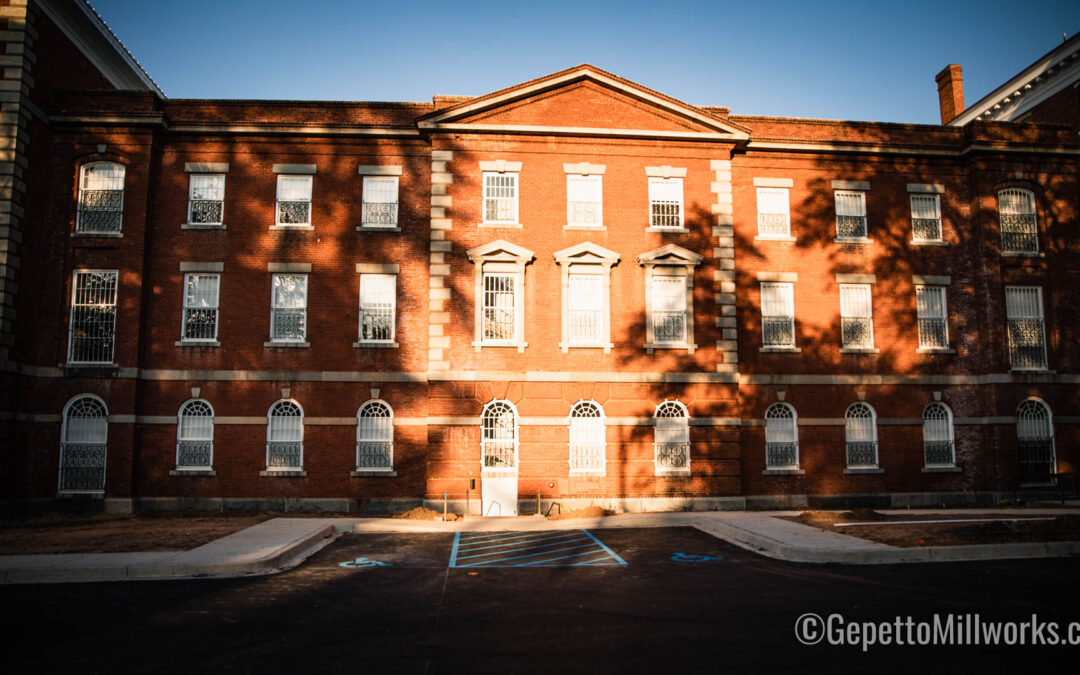
Historic Building Tax Credits
Maximizing Historic Building Tax Credits with Gepetto Millworks’ Authentic Wood Architectural Elements
Restoring historic buildings is both a labor of love and a commitment to preserving cultural heritage. While the process is rewarding, it can also be financially daunting. One significant financial incentive available to property owners and developers is historic building tax credits. These credits can offset the costs of preservation and restoration, especially when using historically accurate materials and techniques.
Gepetto Millworks, a premier manufacturer of authentic wood architectural elements based in Virginia, provides an invaluable resource for those seeking to maximize these tax credits. This article outlines key considerations for qualifying for historic building tax credits and highlights how Gepetto Millworks’ custom-crafted products can be instrumental in achieving compliance with historic preservation standards.
Gepetto Project History of Tax Credit Projects
Understanding Historic Building Tax Credits
Historic building tax credits are financial incentives offered at both federal and state levels to encourage the preservation and rehabilitation of historic structures. These credits reduce the tax liability of property owners who undertake qualified restoration projects.
Federal Historic Preservation Tax Incentives Program
The Federal Historic Preservation Tax Incentives program, administered by the National Park Service (NPS) in partnership with the Internal Revenue Service (IRS) and State Historic Preservation Offices (SHPOs), offers a 20% tax credit for the rehabilitation of income-producing historic buildings. Eligible structures must be listed in the National Register of Historic Places or located in a registered historic district. Arlington VA Historic Window Builder credits are an example of a historic district.
State-Level Tax Credits
Many states, including Virginia, offer additional tax credits for historic preservation. These credits can often be combined with the federal program, providing substantial financial benefits for property owners. In Virginia, for instance, the state’s Historic Rehabilitation Tax Credit program offers a 25% credit for qualifying expenses.
Key Considerations for Filing Historic Building Tax Credits
To qualify for historic building tax credits, property owners must meet specific criteria and follow a structured application process that is often hindered by supplying historic restoration millwork! Here are the critical steps and considerations:
1. Determining Eligibility
- Historic Designation: The building must either be listed in the National Register of Historic Places, contribute to a historic district, or meet specific criteria outlined by the SHPO.
- Income-Producing Property: For federal tax credits, the property must generate income, such as through commercial use or rental housing.
2. Meeting the Secretary of the Interior’s Standards for Rehabilitation
The NPS evaluates projects based on the Secretary of the Interior’s Standards for Rehabilitation, which emphasize retaining and preserving historic character. Key principles include:
- Repairing rather than replacing historic materials.
- Ensuring new additions are compatible with the building’s historic character.
- Avoiding alterations that destroy significant historical features.
3. Qualified Rehabilitation Expenses (QREs)
Only certain costs are eligible for tax credits, including:
- Exterior and interior structural repairs.
- Restoration of historic architectural elements.
- Mechanical, electrical, and plumbing systems integral to the building’s structure.
- Architectural and engineering fees related to the project.
Non-eligible expenses typically include landscaping, new additions, and furnishings.
4. Application Process
The application involves three parts:
- Part 1: Certify the property’s historic status.
- Part 2: Obtain approval for the proposed rehabilitation work.
- Part 3: Certify that the completed work meets approved plans and the Secretary’s Standards.
The Role of Gepetto Millworks in Historic Building Restoration
Gepetto Millworks specializes in manufacturing authentic wood architectural elements that are essential for restoring historic buildings to their original grandeur. Their expertise and dedication to craftsmanship make them a trusted partner for projects seeking historic building tax credits.
1. Authenticity and Craftsmanship
Gepetto Millworks employs traditional techniques and materials to create wood elements that match the original features of historic buildings. From intricately carved moldings to custom windows and doors, their products are designed to seamlessly integrate into existing structures while meeting the Secretary’s Standards.
2. Custom Solutions for Unique Projects
Every historic building is unique, requiring tailored solutions to address specific restoration challenges. Gepetto Millworks offers custom fabrication services to replicate original designs, ensuring accuracy and compliance with preservation guidelines.
3. Sustainable Practices
Sustainability is a core value at Gepetto Millworks. They source premium, responsibly harvested wood and prioritize eco-friendly manufacturing processes, aligning with modern sustainability goals without compromising historical authenticity.
Key Products by Gepetto Millworks for Historic Restorations
Gepetto Millworks’ product offerings encompass a wide range of architectural elements critical to historic restorations. Each product is crafted with attention to detail and adherence to historical accuracy.
Custom Windows
- Historical Accuracy: Gepetto Millworks replicates historic window designs, including sash, casing, and muntin profiles.
- Energy Efficiency: Modern performance standards are integrated into historically accurate designs, ensuring energy efficiency without sacrificing authenticity.
Architectural Moldings
- Period-Specific Designs: Gepetto’s catalog includes moldings that reflect the styles of different historical periods.
- Custom Fabrication: Unique designs can be reproduced to match existing elements precisely.
Doors and Entryways
- Handcrafted Quality: Gepetto’s custom doors capture the elegance and craftsmanship of historic entryways.
- Variety of Styles: Options range from Georgian and Victorian designs to mid-20th-century modern aesthetics.
Staircases and Railings
- Traditional Joinery: Gepetto employs traditional woodworking techniques to craft staircases and railings that embody historical authenticity.
- Custom Components: Balusters, handrails, and newel posts are tailored to the building’s era and style.
Compliance with Preservation Standards
Using Gepetto Millworks’ products in your restoration project can simplify compliance with preservation standards, enhancing your chances of approval for tax credits. Places like Cape Charles, VA 23310 have Historic Building Materials local ordenances that keep the character of the whole town that you would know about as you purchased the property.
Adherence to the Secretary’s Standards
- Repair Over Replacement: Gepetto’s focus on repairing and replicating original features aligns with the Standards’ emphasis on preservation. Our shop built wood products are built with the same solid wood mortise and tenon construction that was used 200 years ago. Most other products you will find on the open market do not use historically accurate building techniques, they shortcut the quality for speed of production in the factory.
- Compatible Materials: Their use of authentic wood ensures compatibility with historic structures.
Documentation Support
Gepetto Millworks provides detailed documentation of their products’ historical accuracy and manufacturing process, which can be included in your tax credit application to demonstrate compliance.
Case Studies: Gepetto Millworks in Action
1. Restoring a 19th-Century Townhouse in Richmond, Virginia
- Challenge: Replacing deteriorated windows while maintaining historical integrity.
- Solution: Gepetto crafted custom wood windows replicating the original sash profiles and integrated energy-efficient glazing.
- Outcome: The project received both federal and state tax credits.
2. Renovating a Historic Church in Alexandria, Virginia
- Challenge: Restoring ornate moldings and woodwork damaged by decades of wear.
- Solution: Gepetto’s team recreated intricate carvings using traditional techniques.
- Outcome: The restoration earned praise from the SHPO and qualified for tax credits.
Steps to Get Started with Gepetto Millworks
- Consultation: Schedule a consultation with Gepetto Millworks to discuss your project needs and goals.
- Design and Fabrication: Work with their expert team to develop custom solutions that align with your building’s historical character.
- Installation Support: Gepetto provides guidance to ensure proper installation and compliance with preservation standards.
- Documentation: Receive detailed documentation to support your historic building tax credit application.
Conclusion
Securing historic building tax credits requires meticulous planning, adherence to preservation standards, and a commitment to quality restoration. Gepetto Millworks’ authentic wood architectural elements are a crucial asset for achieving these goals. By combining traditional craftsmanship with modern sustainability practices, Gepetto Millworks ensures that every project not only preserves history but also meets the highest standards of excellence.
Partner with Gepetto Millworks for your next historic restoration project and unlock the full potential of historic building tax credits. Contact their Virginia fabrication facility today to learn how they can bring your vision to life while honoring the past.
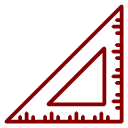
Custom by Architects
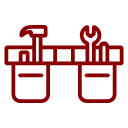
WholeSale to Builders
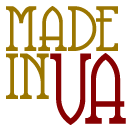
MADE IN VA
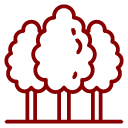